第3回 AIで叶えた倉庫内作業のスマート化
Morimasa Shogo
Morimasa Shogo
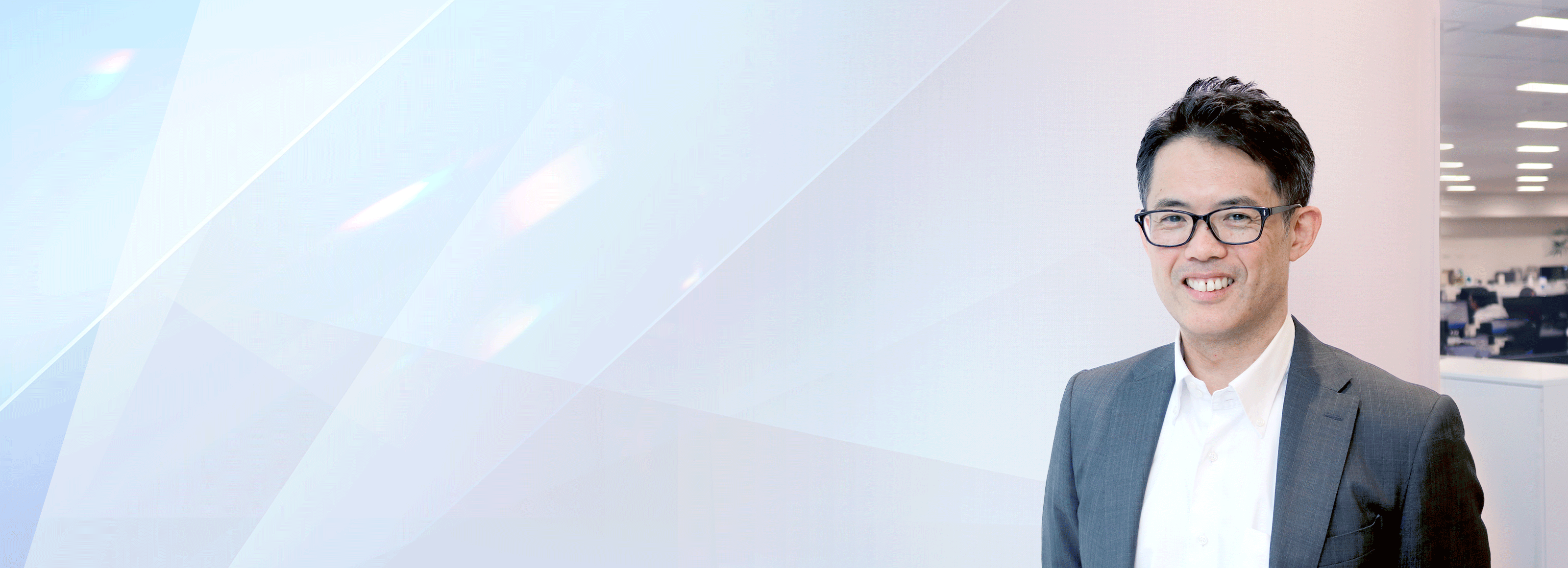
第2回「パートナー企業と連携した輸配送DX」では2024年問題への対応として、輸配送業務全体のデジタル化についての取組みをご紹介しました。今回は、物流業務の中で最も人手が必要となる倉庫内作業の省人化に焦点を当て、AIやロボティクス等の最先端技術を駆使した倉庫内作業の最適化を担う当社ロジスティクスイノベーション室スマートデザイン部門の森政 彰吾が「AIで叶えた倉庫内作業のスマート化」について語ります。
2024年問題はトラックを保有する運送会社だけではなく、物流会社の倉庫内作業の自動化やシステム導入への投資による効率化も重要な解決策の一つだとされていますが、NTTロジスコの物流センターではどのような問題が生じていましたか。
トラックドライバーの時間外労働時間の削減には、荷物の引渡し時間の前倒しや定刻通りの引渡しの徹底が必要不可欠ですが、それらを実現するためには前工程である倉庫内作業の生産性を向上させることが重要です。当社物流センターでは、かねてから作業者の高齢化等に伴う人手不足が問題となっていました。
人手不足への対策は物流業界全体の課題でもありますね。NTTロジスコではそれらの課題に対して、どのようにアプローチしていますか。
当社では、物流センターにおける倉庫内作業の自動化とシステム化による生産性向上に取り組んでいます。私が所属する部署は、全国にある当社物流センターの倉庫内作業における様々な課題を収集し、それぞれの課題に合わせたAI・ロボティクス技術の導入を推進しています。
最先端の技術を駆使して倉庫内作業の効率化を模索されていると思いますが、特に象徴的な取り組みを教えてください。
当社が掲げる「LOPOCE®」※のリソースの1つであるAIを用いて、2021年に「AI画像認識技術を用いた自動検品システム」を自社開発したことですね。本システムは2023年に機能拡張したバージョンアップ版をリリースして、より作業効率性を高めています。
※:「Logistics Process Optimization and Co-evolution Platform(物流プロセス最適化&共進化プラットフォーム)」。NTTロジスコの強みである5つのリソース(AI・ICT、ロボティックス、ネットワーク、ナレッジ、SCM)から収集したデータを相互に統合・活用することにより、サプライチェーンの様々な課題を解決することで、お客様の物流改革・DXを実現し、パートナー企業様と共に進化させる物流基盤。
では、今回は「AI画像認識技術を用いた自動検品システム」について伺ってみたいと思います。システムの導入に至った経緯と概要を教えてください。
IT機器の物流をメインに取扱う埼玉物流センターでは、撤去・回収したレンタル通信機器を再利用するためにクリーニング、動作試験、再セット化作業等を行うリファビッシュサービスを実施しており、およそ100種類の機器本体に2つの付属品(対応する100種類の電源アダプターと、本体設置用の約30種類の台座)を1日約5,000組セット化しています。作業者は、付属品にバーコード等の商品識別子が表示されていないことから、電源アダプターについては印字されているメーカー名や製品モデル名を、台座については形状を目視で確認することにより物品コードを特定し、本体と対になる付属品を判別していました。また、目視による誤判定を防止するため2名体制で検品作業を実施しており、熟練者のスキルと人手を必要とする作業になっていました。そこで人手による作業・熟練者に作業の属人化からの脱却を目指し、このシステムを開発・導入しました。
当システムは、カメラが機器本体の製造番号を表示するバーコード、電源アダプターの製造モデルを表す文字情報と台座の形状の3点を同時に撮影し、撮影画像をシステム内でAIにより画像認識処理を行い、電源アダプターと台座の物品コードを取得、登録済みのマスタデータと照合し合致した場合、当システムからWMS(倉庫管理システム)に取得したテキストデータを送信することにより、従来の目視検品作業を自動化するものです。
開発当時、認識対象の機器本体・電源アダプター・台座の3種類の再生品をそれぞれの特徴に最適な認識方法を用いて同時認識できるサービスがなかったこと、またシステムの継続的なデブオプスを見据えて、自社での開発を決断しました。
開発にあたって、苦労したことはありましたか。
最も苦労したのは、再生品の特徴に合わせたシステム開発です。再生品は新品とは異なり、同じ製品でも製造年や使用状況によって微妙に外観の状態が異なります。例えば、同じ製品の台座でも製造年によって僅かな素材の違いがあったり、使用状況で傷や色あせがあったりしますが、これらをシステムに「同一」の製品だと正しく認識させる必要があります。単純に認識精度を上げ過ぎると、かえって同じ製品を「別物」と判断してしまう恐れもあるので、製品毎の一致率の基準を定めることが大変でした。また、照明の明るさや方向、商品の置き方によって認識結果が変わってしまうため、様々な条件下でテストを繰り返し、様々な製品に対して一定の認識精度を保ちつつ、かつ作業者が撮影台に再生品一式をセットしやすい配置等の条件を検証し、作業者の意見を聞きながらシステムの改良を重ねました。
システム導入により実際にどのような効果が得られましたか。
作業品質確保のために従来2人1組での作業体制を取っていましたが、システム導入により完全セル化し1人での作業が可能となり、また作業人員数を従来の16名から7名へ9名削減し、目標としていた人手不足の問題を解消することが出来ました。さらに作業の生産性も90%向上し、自動化により検品ミス0%も実現しました。システムの導入により、高齢化が進むベテラン作業員が退職しても、熟練者に依存しない作業体制を構築することが可能となり、セット化検品作業の永続性を担保することができました。
当システムの開発・導入で得たノウハウは他にどのような業務に展開することができますでしょうか。
現在この技術を別工程である再生品の受入れ時の仕分け作業に応用し、さらなる倉庫内作業の自動化を進めています。セット化検品作業で培ったノウハウが、この新たな自動化プロジェクトの企画・実現に大きく貢献しています。また、全国の他物流への展開も進めているところです。
今後の展望について教えてください。
AIやロボティクスの技術は日々進化しており、物流分野における活用の可能性は今後ますます広がっていくと考えています。今後は、AI画像認識技術だけでなく、生成AIを中心とした他のAI技術も積極的に活用し、より高度に自動化されたスマートで持続可能な物流現場の実現に挑戦していきたいと考えています。
ありがとうございました。
森政 彰吾(もりまさ しょうご)
ロジスティクスイノベーション室 スマートデザイン部門 担当課長、
応用情報技術者、G検定(日本ディープラーニング協会)
AI画像認識技術・マテハン機器等、AI・ロボティクスをベースとした業務の自動化・DX化を推進